Understanding, modeling and improving the development of complex products : method and study
Author(s)
Rogers, Bradley W. (Bradley Warren)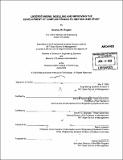
DownloadFull printable version (34.90Mb)
Other Contributors
Leaders for Manufacturing Program.
Advisor
Deborah Nightingale and Steven D. Eppinger.
Terms of use
Metadata
Show full item recordAbstract
Development of new aerostructure designs frequently occurs through a complex process that is difficult to understand and control. Tight requirements for weight, cost, strength, and aerodynamic behavior create many interdependencies in the product design, which translate through to the design process. An increasing fragmentation of the commercial aerospace industry has also added a dimension of complexity to the process - outsourced component designs are often interdependent with in-house component designs, resulting in frequently changing requirements for supplier components during the design process. This thesis offers an analysis of the product development processes of a first-tier aerostructures supplier, Spirit AeroSystems. Although this host company provides the context for analysis, the method is meant to be generally applicable to the development of any complex product. The Design Structure Matrix (DSM) methodology is used to capture the required interaction between tasks of the development of a propulsion structure for commercial aircraft. The task times, time variations, work loads, interdependencies, likelihoods of rework, and learning curves are then quantified and applied to a discrete-event Monte Carlo simulation model which outputs probabilistic completion time and workload of the project. The model is then used to show how changing the customer requirements at different points in the development cycle affect the cost and schedule of development. (cont.) The failure modes and effects analysis (FMEA) is applied to quantify risks and ensure proper control of their likelihoods and consequences A holistic industry-level analysis provides insight into the complexities of developing an interdependent product across multiple organizations. Potential recommendations to improve the development process are outlined. Finally, the "Three Lens" methodology is applied to identify implementation obstacles. This paper builds upon product development process simulation theory by introducing process independent externalities into the model to show how changing customer requirements may impact the cost and schedule of development. It also proposes a new framework for optimal staffing based upon the maturity of the customer requirements. Finally this paper shows that a disintegrated, sections-based design process architecture, like that used for the Boeing 787, is sub-optimal for product development, and it proposes a new architecture for developing aircraft.
Description
Thesis (M.B.A.)--Massachusetts Institute of Technology, Sloan School of Management; and, (S.M.)--Massachusetts Institute of Technology, Engineering Systems Division; in conjunction with the Leaders for Manufacturing Program at MIT, 2009. Includes bibliographical references (p. 90).
Date issued
2009Department
Leaders for Manufacturing Program at MIT; Massachusetts Institute of Technology. Engineering Systems Division; Sloan School of ManagementPublisher
Massachusetts Institute of Technology
Keywords
Sloan School of Management., Engineering Systems Division., Leaders for Manufacturing Program.