CASE STUDY: From Three to One: Integrating a High Performance Work Organization Process, Lean Production, and Activity Based Costing Change Initiatives
Author(s)
Kochan, Thomas A.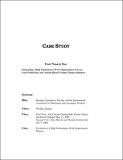
Download2000_Kochan_FromThreetoOne.pdf (335.4Kb)
Terms of use
Metadata
Show full item recordAbstract
In 1997 Boeing’s Wichita Division and the International Association of Machinists and Aerospace Workers agreed to launch a “High Performance Work Organization” (HPWO) process. This followed the introduction of a Lean Production Initiative in 1994-95 and an Activity Based Costing (ABC) initiative in 1996. Managers and union leaders in Wichita sought to sustain and grow each of these change and improvement efforts in ways that empower the workforce and enhance the competitiveness of the operations. Although these initiatives share some similar objectives and could potentially serve to complement and reinforce each other, to date they have been led and managed separately. Each is experiencing a slow and difficult path of diffusion. The key challenge facing management and union leaders is to decide how to best integrate these separate improvement programs into a single, focused initiative that builds broader awareness, support, and demand for its features across all levels of the workforce and the management and union organizations in the Wichita operation. Given the combination of the engineering culture of Boeing and the pragmatic orientation of the workforce in Wichita, the parties may want to shift to a more targeted task or problem specific approach that engages a broad cross section of hourly workers, engineers, and managers in specific improvement initiatives. Doing so might shift from a top-down supplier push to a distributed, demand-pull process of innovation and adaptation.
Date issued
2000Keywords
high performance work organization, HPWO, activity based costing, ABC, lean production initiative, Boeing
Collections
The following license files are associated with this item: