Active control of rotating stall in axial compressors
Author(s)
Paduano, James D. (James Donald)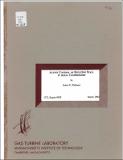
Download28801772.pdf (15.36Mb)
Other Contributors
Massachusetts Institute of Technology. Gas Turbine Laboratory
Metadata
Show full item recordAbstract
An active control system has been implemented on a low-speed single-stage axial compressor. This control system stabilizes the perturbations which normally lead to rotating stall, thus extending the range of operation of the compressor to a flow coefficient 23% below the natural stall flow coefficient. Sensing of the perturbations which precede stall is accomplished using a circumferential set of hot wires mounted at an axial station ahead of the rotors. Actuation is accomplished by a set of 12 high-response inlet guide vanes, whose individual deflections can be controlled independently by a digital computer. The feedback scheme used in this work is motivated by a recently developed model for rotating stall. In this model, the perturbation axial velocity as a function of circumferential position at any axial station completely determines the state of the system. Furthermore, circumferential sinusoidal waves of the perturbation are the fundamental eigenmodes, and these eigenmodes develop as rotating waves around the annulus. When the eigenvalues associated with these eigenmodes become unstable, the system diverges into rotating stall. Therefore, feedback stabilization of these rotating waves is used as the technique to eliminate rotating stall. The model for rotating stall is extended to include the effects of high-response inlet-guide-vane actuation. This model is then converted from a system of partial differential equations (PDEs) to a set of ordinary differential equations (ODEs). This conversion will be shown to yield a model to which standard control and identification techniques can be applied. The experimental investigation consisted of two main parts. The first part is systematic identification of the relevant compressor dynamics. The procedures described yield an accurate model of the compressor input-output behavior over the frequency range of interest (DC to twice rotor rotation frequency), for flow coefficients which span the entire range of stable and unstable (stabilized) operation of the system. This identification verifies the basic behavior predicted by the model and provides quantitative information for control system design. The second part of the experimental investigation is active stabilization. The goal of active control is to extend the range of the compressor to the lowest flow coefficient possible. It is shown that, in the compressor studied, the circumferential sinusoidal modes go unstable in succession - first mode, followed by second, followed by third, as flow coefficient is reduced. Thus, additional range of the compressor is gained for each additional mode stabilized.
Description
March 1992 Includes bibliographical references (p. 231-233)
Date issued
1992Publisher
Cambridge, Mass. : Gas Turbine Laboratory, Massachusetts Institute of Technology, [1992]
Series/Report no.
GTL-208GTL report #208